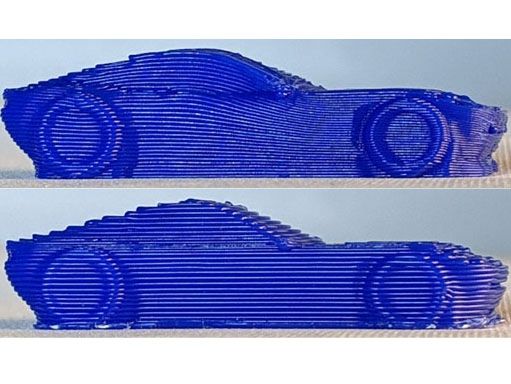
La fabrication d’objets par impression 3D s’est largement démocratisée et de nombreuses imprimantes à fil fondu (Fused Filament Fabrication ou FFF) sont désormais disponibles chez les professionnels de la CAO, dans les FabLab, les écoles, mais aussi chez les particuliers passionnés par cette technologie. Un défaut souvent produit par l’impression 3D est l’effet "d’escalier" qui apparaît le long des surfaces supérieures légèrement inclinées : le "dessus" de pièces courbes. Il nécessite souvent un ponçage manuel pour obtenir un résultat lisse.
« Nous voulions optimiser la fabrication d’objets légèrement arrondis sur l’imprimante à filament de Monsieur Tout le Monde », précise Sylvain Lefebvre, directeur de recherche Inria et responsable de l’équipe MFX.
Repenser les paramètres d’impression
Pendant longtemps, cette imperfection des objets à surfaces en faible pente a été considérée comme inhérente à la technologie de fabrication elle-même, puisqu’elle consiste à déposer progressivement de la matière par empilement de couches planes, chacune d’épaisseur uniforme. Pour cela, l’objet désiré est d’abord modélisé en 3D puis un logiciel établit la suite d’instructions de déplacements horizontaux à donner à la tête d’impression pour fabriquer chaque couche.
Il est cependant aussi possible de déplacer la buse d’une imprimante à filament classique à la verticale, pour qu’elle dépose le long de courbes. Cette possibilité est rarement exploitée car il est difficile d’obtenir un algorithme décomposant une pièce en tranches courbes sans introduire un risque de collision entre l’imprimante et la pièce en cours de fabrication. Il faut également respecter d’autres contraintes, comme des épaisseurs de dépôt minimum et maximum. Jusque-là aucun algorithme ne permettait aux imprimantes classiques de tirer partie de ce déplacement vertical.
En collaboration avec des chercheurs d’Allemagne, des États-Unis, du Canada et de Hong-Kong, les chercheurs des équipes MFX et Pixel ont créé un tel algorithme. Il permet de faire varier progressivement la hauteur de la buse d’impression et l’épaisseur des dépôts, tout en garantissant qu’aucune collision ne se produira. Ainsi, à partir de la modélisation 3D de l’objet, ils peuvent programmer le dépôt de matière suivant les pentes naturelles de la pièce (inférieure à 30°), et non plus tranche horizontale par tranche horizontale.
En se basant sur la forme finale de l’objet à imprimer, l’algorithme optimise la trajectoire de la buse d’impression et les dépôts en tenant compte des différentes contraintes que sont la présence de pentes douces, l’encombrement de la tête de la buse et le risque de collision de celle-ci avec de la matière déjà déposée. L’algorithme produit ainsi une série d’instructions non seulement dans le plan horizontal (x,y) mais également en jouant sur l’altitude (z) de la buse et la quantité de matière déposée en chaque point, ce qui permet de déposer des couches d’épaisseurs variables.
L’Open Access pour un plus grand impact
« L’algorithme permet d’obtenir des objets dont les pentes faibles sont grandement améliorées, sur les imprimantes 3D existantes », se réjouit Sylvain Lefebvre.
Seul point négatif : ce nouveau procédé implique un temps de calcul de la trajectoire de la tête un peu plus long (il faut quelques minutes - et non plus quelques secondes - pour calculer la trajectoire de la buse). Ce délai est cependant raisonnable au vu de la qualité du résultat obtenu : une surface lisse est moins fragile qu’une surface rugueuse et l’obtenir dès la fin de l’impression signifie que l’étape de lissage finale en est largement allégée. Finalement, le travail est plus précis pour un même nombre de tranches, avec un gain de temps et un gain en résistance lors de l’utilisation.
Pour qu’il ait un impact positif le plus large possible, cet algorithme, décliné en logiciel nommé CurviSlice, sera mis à disposition sous forme de code source pour que les utilisateurs d’imprimantes 3D puissent s'en emparer.
SIGGRAPH
SIGGRAPH (Special Interest Group on Computer GRAPHics and Interactive Techniques) est une conférence internationale majeure sur l'infographie : elle regroupe chaque année depuis 1974 un grand nombre d’acteurs industriels, artistiques et scientifiques de l’univers de l’image de synthèse, qu’il s’agisse de films d’animation, de création d’effets spéciaux, de jeux vidéos ou de logiciels permettant la modélisation 3D. L’édition 2018, qui s’est tenue à Vancouver, a rassemblé 16 500 participants venus de 88 pays.
La 45e édition de SIGGRAPH se tiendra au Convention Center de Los Angeles du 28 juillet au 1er août et l’équipe MFX, commune à Inria et au Loria, y présentera trois articles scientifiques. Les résultats présentés portent sur de nouveaux algorithmes optimisées pour la conception et l’impression 3D de dépôts courbes sur imprimantes à filament standard, de métamatériaux basés sur des géométries polygonales en étoiles et de motifs structurés anisotropes à gradient de propriétés physiques.
Le logiciel CurviSlicer sera présenté à la conférence SIGGRAPH, session "fabrication", le 31 juillet à 11h29 salle 150/151.
En savoir plus
Lire aussi
L’article scientifique CurviSlicer: Slightly curved slicing for 3-axis printers