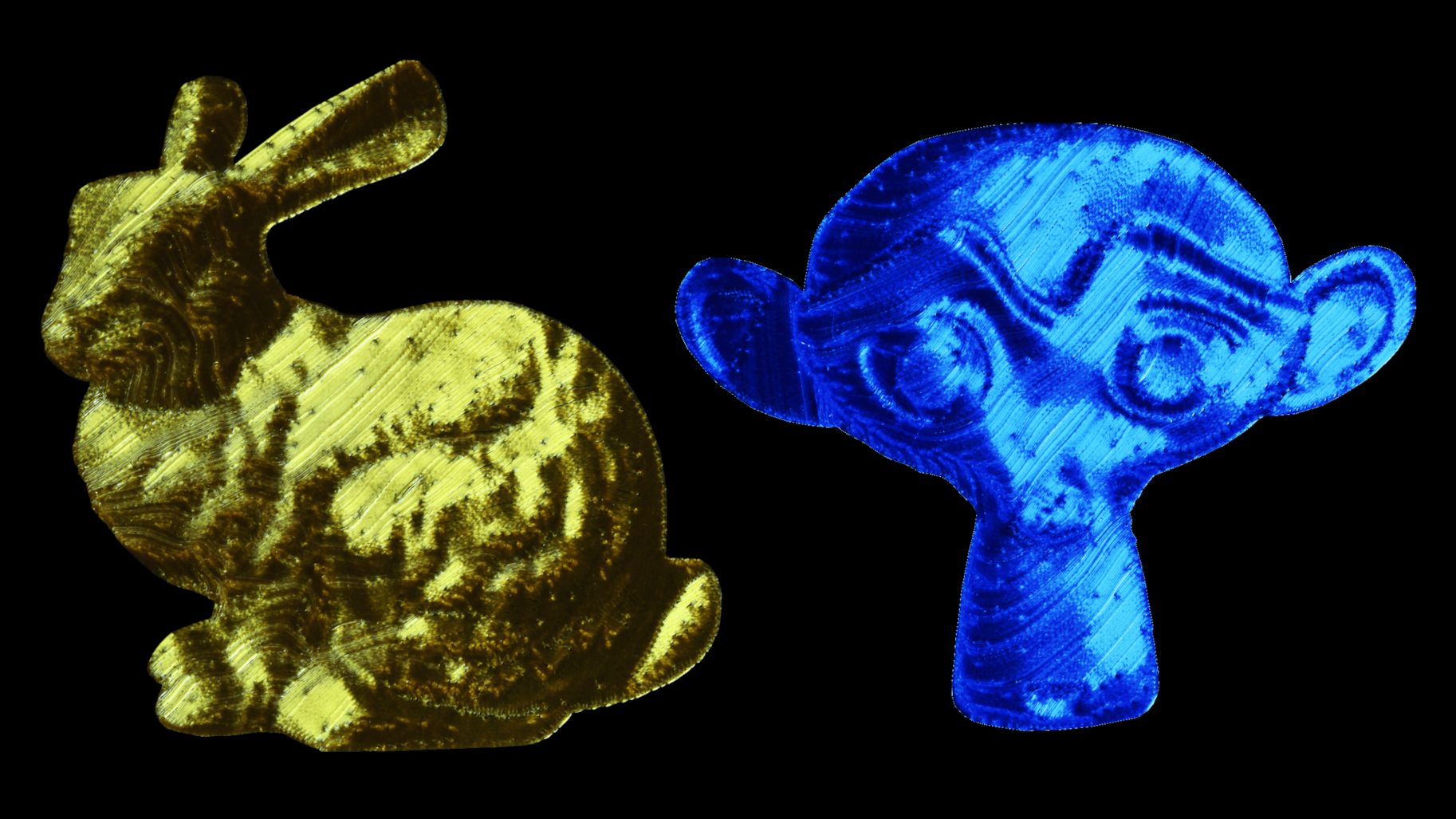
3D printed surfaces for the art world
3D printing processes (or additive manufacturing) are constantly developing and finding uses in a wide range of industrial sectors. They can be used to produce parts in a variety of shapes, and are of particular interest to the aerospace, automotive and medical industries. The innovations recently developed by researchers on the MFX team, in collaboration with Inria and Loria (the Lorraine IT research laboratory), have found a new - and particularly original - field of application: creation and design.
With his colleagues from MFX, Xavier Chermain, recently recruited by Inria, has succeeded in creating flat 3D printed surfaces with an appearance similar to that of brushed metal. This material is used in the design of many everyday objects, such as bistro tables, with patterns made by circular brushing of aluminium that gives them a unique appearance - and a very attractive shine.
Xavier Chermain, an expert in appearance models
Xavier Chermain joined Inria in 2022, after completing a postdoctorate the previous year with the MFX team, to which he brought new skills in appearance modelling. He has been interested in this subject since his thesis, conducted at the X-LIM laboratory (University of Limoges) from 2015 to 2019, followed by two postdoctorates at the University of Strasbourg (with the IGG (Geometric and Graphic IT) team at the ICube laboratory) from 2019 to 2021. His research, which has contributed to the development of image synthesis algorithms for the visual industry (special effects, video games, etc.), also has applications in the field of surface rendering simulation.
Robust algorithms for modelling and reproducing using commercially available equipment
This research, which will be presented by the young researcher in Los Angeles in August at the Siggraph 2023 international conference, is remarkable in more ways than one. Based on advanced digital modelling and particularly robust algorithms, the method developed by the MFX team makes it easy to reproduce the look of brushed metal with commercially available equipment. What's more, it makes the technique accessible to the general public at a low production cost!
Xavier Chermain highlights the originality of this research: “MFX has developed unique skills in 3D printing, using recent developments in computer graphics and appearance rendering. The project team has developed algorithms capable of very precisely controlling the deposit of material by additive manufacturing machines: this means that we can control the roughness of a surface on a very small scale, which determines its appearance.”
A long history of expertise
This innovation is largely a result of the expertise developed by the young researcher in modelling and appearance rendering (see insert) prior to his arrival at Inria. Xavier Chermain had developed digital models to predict the appearance of a material. The presence of microscopic bumps has a major influence on the appearance of a surface: the smoother it is, the brighter and more reflective it appears; the rougher it is, the more diffuse its reflections.
In theory, we can make an object sparkle more by controlling the distribution and orientation of these bumps, which form a myriad of micro-facets. Thanks to computer simulation of the many reflections of light by all these tiny mirrors, we can calculate the overall appearance of the object. In practice, however, several hundred thousand - or even several million - light paths need to be modelled to obtain a convincing result. Modelling appearance rendering is therefore extremely time-consuming and impractical in real-life situations.
Modelling and predicting rendering
How can this be done? “I was interested in “implicit” modelling of appearance rendering, which considerably reduces calculation times,” explains Xavier Chermain. “These approaches are being developed in computer graphics, for example for special effects applications, which require real-time simulations. They are based on statistical processing of the characteristics of the micro-facets (number, size, orientation) to determine the rendering of surfaces. I have developed an algorithm to predict the overall appearance of a surface based on its microscopic state.”
“Implicit” modelling makes it possible to define a priori the characteristics of the material required for the desired rendering, such as sparkle. And this is where the MFX team's expertise comes into play: the researchers then couple the appearance rendering simulation with the algorithms driving 3D printing, developed some time ago by the IceSL software.
“By using a special process called wire deposition, we can deposit fine filaments of plastic in a given orientation to obtain the shiny appearance of metal,” explains the researcher. “We work with commercially available printing equipment, which only costs a few hundred Euros. In this way, we make it easy to create a distinctive look that is usually difficult to produce, as brushed metalwork requires highly specialised tools and skills. The only constraint in making the object is to use our algorithm, which will soon be available to the general public.”
For advertising, design, film and building!
From artistic creation to architecture, design and advertising, the areas of application for this process are endless! Some examples? We can imagine promotional materials with a unique appearance (a creative mind will then devise an appropriate marketing strategy for these objects!), or set or costume pieces for the cinema, such as armour or swords with magnificent reflections for the next successful Heroic Fantasy series.
“With our method, it is also possible to prototype new objects very quickly before launching industrial production using conventional techniques (such as metal brushing), or to create models of buildings with metal facades featuring specific patterns,” explains Xavier Chermain.
The inventive researcher intends to demonstrate the merits of this innovation by example: before flying off to the United States in August to present his work, he is going to print business cards on a sparkling material with the logos of MFX, its host laboratories and a QR code linking to the team's website. There is no doubt that this approach, along with his presentation, will attract attention and interest, with a view to future scientific collaboration!
Find out more
- IceSL : Printing freely in 3D, Inria, 18/10/2019.
- An algorithm for creating high-contrast irregular patterns, Inria, 22/07/2019.