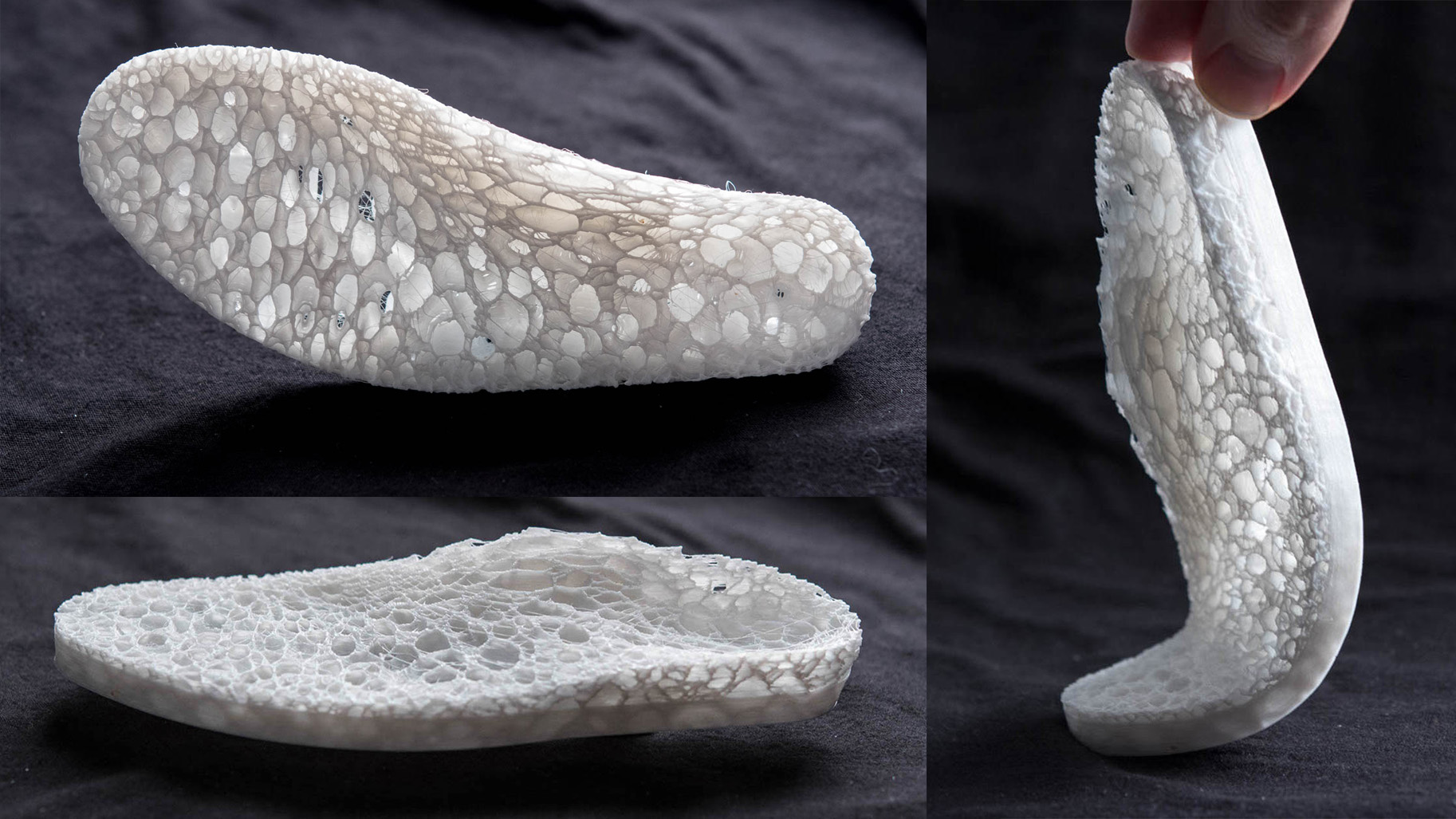
Pushing the boundaries of additive manufacturing
The booming field of 3D printing (or additive manufacturing) has attracted interest from a range of different industrial sectors as progress is made towards the factories of the future. By adding materials one after the other, this particularly innovative method can be used to build objects in a range of shapes and sizes, addressing needs in the aeronautics industry, the space industry, the automobile industry and the medical sector.
It was also central to MuFFin (Microstructures procédurales et stochastiques pour la fabrication fonctionnelle - Procedural and stochastic microstructures for functional manufacturing), a project led by Jonàs Martínez, who is a researcher with the MFX project team at the Inria Nancy - Grand Est Centre. Funded by the ANR as part of the “Young researchers” programme, it is one of the few projects on designing metamaterials to have involved Inria researchers. What made it so original was that by aiming to push the boundaries of additive manufacturing, MuFFin developed a way of printing components using foam whose physical components can be controlled. This also led to a collaboration with Defrost, a project team at the University of Lille Inria Centre, on applications in soft robotics.
Tailoring the physical properties
Jonàs Martinez outlines the main advantage of 3D printing: “It allows you to produce structures on a small scale which can alter the performance of objects on a large scale. For example, you can use a computer to design structures with mechanical characteristics not found in traditional materials (such as steel, wood or concrete) and then produce them using additive manufacturing. This has applications in a wide range of fields, and has attracted interest from the worlds of research and industry.”
Most materials used on a daily basis in industry have mechanical properties which manufacturers use to their advantage: the ability to withstand impact, to bear heavy loads, to change shape without breaking, and so on. With additive manufacturing, these properties - which are determined by the microscopic structure of the material - can be “made to order”. These are what are known as “metamaterials”.
Here’s an example. It’s possible to produce a material whose rigidity - its capacity to withstand changes in shape - varies depending on the direction of the load. This material will change shape for a specific orientation, a property which can be utilised in order to control the movement of a structure.
An innovative project in materials science
However, as Jonàs Martinez explains, there is one downside to this digital simulation method: “You can carry out calculations to configure the process you intend to use and determine the desired characteristics for the component. But when you're looking to produce particularly large objects and you need to describe the microstructures of materials in detail, you can soon end up with vast quantities of data.”
How can these limitations be overcome? How can printing be carried out on a large scale while controlling structures on a very small scale? The answer lies in implicitly representing their geometric properties, which can help to reduce storage costs, and in simulating the process layer by layer, helping to reduce memory access during processing. Jonàs Martinez’s research led to the development of a specific module in the IceSL software developed within MFX. It also resulted in the production of a “stochastic foam” featuring random inclusion sizes, like bubbles of air in muffin batter.
A unique range of mechanical properties
In pursuit of this goal, the researcher used simulation models to characterise the mechanical response of the foam, designing an algorithm that could be used to automatically and efficiently cut the microgeometries obtained. Printed using material extrusion technology, these microgeometries offer a unique range of mechanical properties.
Published in ACM Transactions on Graphics, the leading specialist journal on computer graphics, the results sharpened the imaginations of creators. In a subsequent article in joint work with Thibault Tricard and co-authors from MFX, a fibre-like metamaterial also found applications in a graphics rendering engine and featured in a scene in Star Wars 9!
A first application in soft robotics
Jonàs Martinez’s research also attracted interest from the Defrost project team at the University of Lille Inria Centre. Their work is focused on soft robotics, the aim of which is to develop deformable robots. One of the uses of deformable robots is for handling fragile objects or exploring difficult to access cavities. These robots have attracted interest from a range of sectors, including the medical sector.
“We immediately sensed that the material developed by Jonàs Martinez had real potential for controlling a robot”, explains Olivier Goury, research fellow with Defrost. “Following the publication of his article in 2018, we quickly got in touch with MFX in order to assess the potential of this innovation for our applications.”
A successful example of knowledge transfer
Félix Vanneste, a PhD student with the Lille-based team, was the first to learn how to use the tools developed at the Inria Nancy - Grand Est Centre. After a few weeks working with MFX, he had familiarised himself with IceSL, and had learned how to produce a sample of stochastic foam and utilise the remarkable properties of this material.
Olivier Goury, co-director of the research alongside Christian Duriez, was extremely pleased with the results: “The gamble paid off: the robot that was designed using stochastic foam boasts mechanical properties that would never have been possible with the materials traditionally used in soft robotics, such as silicon”. Off the back of this collective achievement, the two teams published a joint article in the journal IEEE Robotics and Automation Letters.
After 42 months of research, MuFFin came to an end in June 2022, having made some remarkable breakthroughs: designing an innovative material, a new software component, a 3D printing process and making it possible for robotics engineers to create materials ready for immediate use.
A number of use cases, suggested by Defrost researchers and published by Félix Vanneste following his PhD (which he was awarded in June 2022), underline how successful this knowledge transfer has been. Just like the sweet treat it was named after, MuFFin took on a range of different appearances...with more than a few surprises along the way.
Verbatim
I worked alongside Jonàs Martinez, helping him to develop algorithms for designing and printing complex microstructures in either 2D or 3D. An interesting facet of his research was the way he brought together knowledge from computer graphics - which is what his background is in - and mechanics: this sort of multidisciplinary work is rare. His research demonstrated real scientific quality, and will be of use to two communities, with an impact going beyond his own field. The microstructures and algorithms which he developed are now used by mechanical engineers and physicists who are also interested in other properties of materials, whether magnetic, thermal or electrical.
PhD, Ecole Polytechnique
Find out more
- Anisotropic soft robots based on 3D printed meso-structured material, video Defrost Soft Robots, 2020.
- Audio interview: Bringing robotics and origami together, with Dewi Brunet and Olivier Goury, podcast, Inria, 23/2/2022.