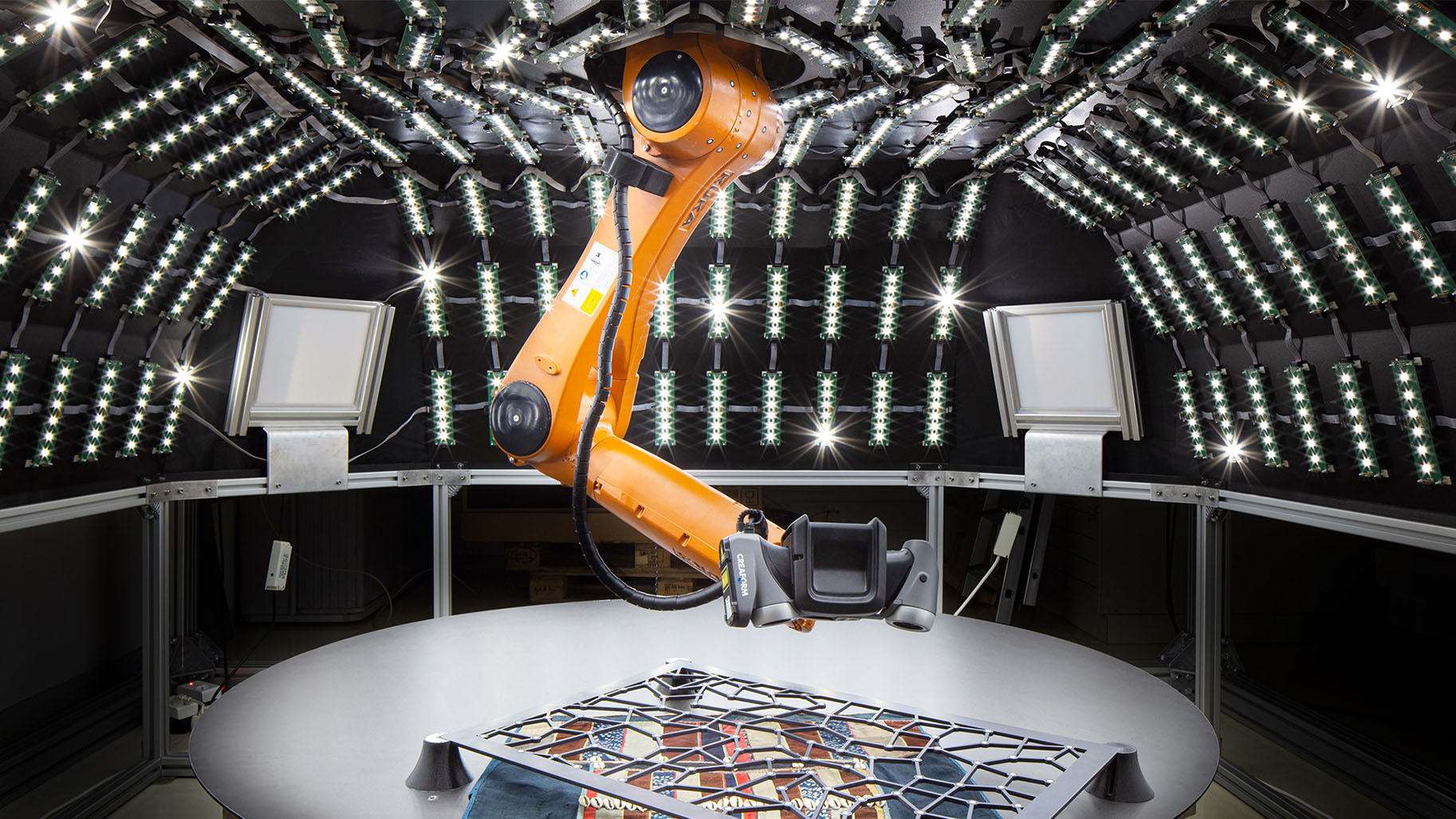
How can rare and fragile clothing of great value from a heritage point of view be suitably showcased? This question gave rise to the Material project, supported by the French National Research Agency. The need was formulated by the Museum of Ethnography of the University of Bordeaux (MEB) more than ten years ago and has now been provided with a solution thanks to technologies developed by two joint Inria project teams (Manao and Maverick) with the University of Bordeaux (LaBRI), the University of Grenoble-Alpes and the CNRS.
The programme, which aims to faithfully digitise the appearance of ancient fabrics and print them in 2.5D, has set itself the objective of developing tools for the acquisition, visualisation and reproduction of conserved artefacts. This multidisciplinary project combines different approaches and calls on the expertise of ethnologists, computer scientists, mathematicians, physicists and industrialists. This collaboration between "hard” sciences and social sciences is reflected in the composition of the collective.
ANR Materials in figures:
3
PhD students
10
researchers
2
engineers
1
textile expert
2
ethnologists
12
hours of scanning time for 1 m²
2 600
km covered
14
articles published
Of the 480 textile artefacts that make up the University of Bordeaux's (MEB) collection, eight were chosen to be digitised, of which three in full, on the basis of their unique motifs and rarity. The process is a complex one that requires detailed study of the height, width and volume of the items, most of which come from South-East Asia and date from the 19th century.
The digitisation of these garments and the production of relief facsimiles helps facilitate the study and transmission of the items and allows us to document the materials used as well as the production, assembly and decoration techniques, while limiting their handling
explains Solenn Nieto, MEB Collections Manager. Reproducing the appearance of an object and representing the different materials it is made of is somewhat of a challenge. Because of their texture, appearance and mechanical properties, the digitisation of these fabrics is no small task. From a heritage point of view, the acquisition procedure must have minimal impact on the objects, which must not be handled.
A scientific, technical and human challenge
Appearance is at the heart of Manao’s research project. It is defined by a combination of three things: light, shape and the material the object is made of. The textiles in the MEB’s collection produce various optical effects that are of interest to us: reflections from the gold threads and metal buttons, anisotropy of the wefts of the fabrics, clusters of layered threads, variations in patchwork patterns, etc. It is this diversity and the wealth of reflections of the materials that makes the ANR project so challenging.
Romain Pacanowski is a Research Engineer at the CNRS and an associate member of the Manao project team. Attached to the Photonics, Numerical and Nanosciences Laboratory (LP2N) - overseen by the University of Bordeaux, the Institut d'Optique Graduate School and the CNRS - Romain supervised the development of an acquisition platform that allows the virtual reproduction of the appearance and shape of extremely fragile heritage items. For instance, the natural fibres of the textiles are sensitive to variations in moisture or exposure to ultraviolet (UV) rays, so capturing the complexity of their appearance is limited by these requirements. A list of specifications was drawn up in order to meet the conservation and promotion aims.
Specifications
- Any materials coming in contact with the item must be chemically neutral.
- The item must remain motionless in the same position during the measuring.
- It must not be subjected to any mechanical stress.
- Constant stability of the moisture, air pressure and temperature conditions must be ensured.
- Ultraviolet and infra-red light are prohibited.
- Exposure time to visible light is limited.
- The device must be able to be used by a non-specialist after training.
These specifications laid the foundations for drafting the prototype and guided the choice of materials. This work was made possible thanks to the PhD by Antoine Lucat. The PhD student combined expertise in optics, mathematics, programming and robotics to design a digital acquisition platform with the aim of reproducing the MEB’s collection in the most realistic way possible.
Reproducing the wealth of details perceived by the eye
It took five years of research and design, with the help of in-house staff and industrial actors, to come up with a prototype that can be divided into five main parts:
- An LED dome. 1,080 white LEDs evenly distributed over a dome. The light can be directed by selecting which LEDs to switch on.
- A camera. With its 12-megapixel colour sensor, this camera has a high frame rate that can capture up to 100 frames per second. It is equipped with a 35mm lens. The device therefore can focus on details in the order of 50μm at the minimum focusing distance.
- A 3D scanner. This device, which uses laser scanning, has a theoretical accuracy of 30μm announced by the manufacturer. It allows measurements of the surface to be obtained in spite of the effect of light reflections.
- A 6-axis robot. With a range of 1.1m, it allows any material to be placed in the dome and has a very high accuracy of 100μm announced by the manufacturer. Its role is to move the camera and the 3D scanner.
- A rotating table to hold the specimen. The table supports the object and allows it to rotate in the horizontal plane, providing an additional degree of freedom.
The prototype in figures:
850 kg
Total weight of the digitisation prototype
2,4 m
Diameter of the dome
1,2 milliard
Weight of the robotic arm
70 kg
Measurement accuracy
0,05 mm
Diameter of the scanning disc
18 750 Blu-ray
Storage size for an area of 1m²
1,48 m
Diameter of the scanning disc
Once the scan is complete, the data is processed for storage and viewing on a computer. The measuring accuracy required to preserve the details of the textiles requires a large storage capacity. It involves capturing the behaviour of light for every 0.05mm on a piece of fabric that can be up to 3m² in size. A multitude of reflections are recorded to reproduce the acute vision of the human eye, capable of distinguishing details of the order of 100 μm. Although scanning takes no more than a few hours, it requires a huge storage capacity (2,400To or 18,750 blu-ray). This is one of the major challenges of the project. Because the data is so big it has to be compressed while preserving the properties of the appearance of the original material as much as possible.
The team has therefore developed a method of material analysis to store the large amount of data acquired by Manao. The solution offers an extremely fast method for measuring, since this process must not exceed the exposure time of one day. The quality of the measurement is independent of the acquisition system in order to guarantee the variety of data stored and to ensure its long-term durability. Induction acquisition methods were therefore chosen in order to reduce uncertainties and obtain the desired accuracy.
Future prospects
All these processes, from calibration and the acquisition of large artefacts to coupling 3D scanner technology with a camera, make this prototype a highly innovative object. It is a solution that could be extended to other museum institutions for heritage conservation and preservation purposes.
In spite of its large size, the prototype has been designed to be transportable. It also offers the advantage of considerable autonomy both during calibration and measurement. It can be handled by a single person, whose presence is only required at two points in the process, and can execute sequences of protocols by itself without the need for human intervention. Above all, however, the scientists want to concentrate their research on processing the data obtained in order to provide precise information about what has been digitised and further develop the algorithmic and mathematical techniques.
The aim is to achieve a speed of 1,500 billion measurements per hour, which corresponds to 4.6To of data. Lastly, to take things further, acquisition and joint digital design could be developed:
My aim is to obtain acquisition protocols in situ and work on complex materials like jade or hide, which have even more complex light reflection properties
concludes Romain Pacanowski.